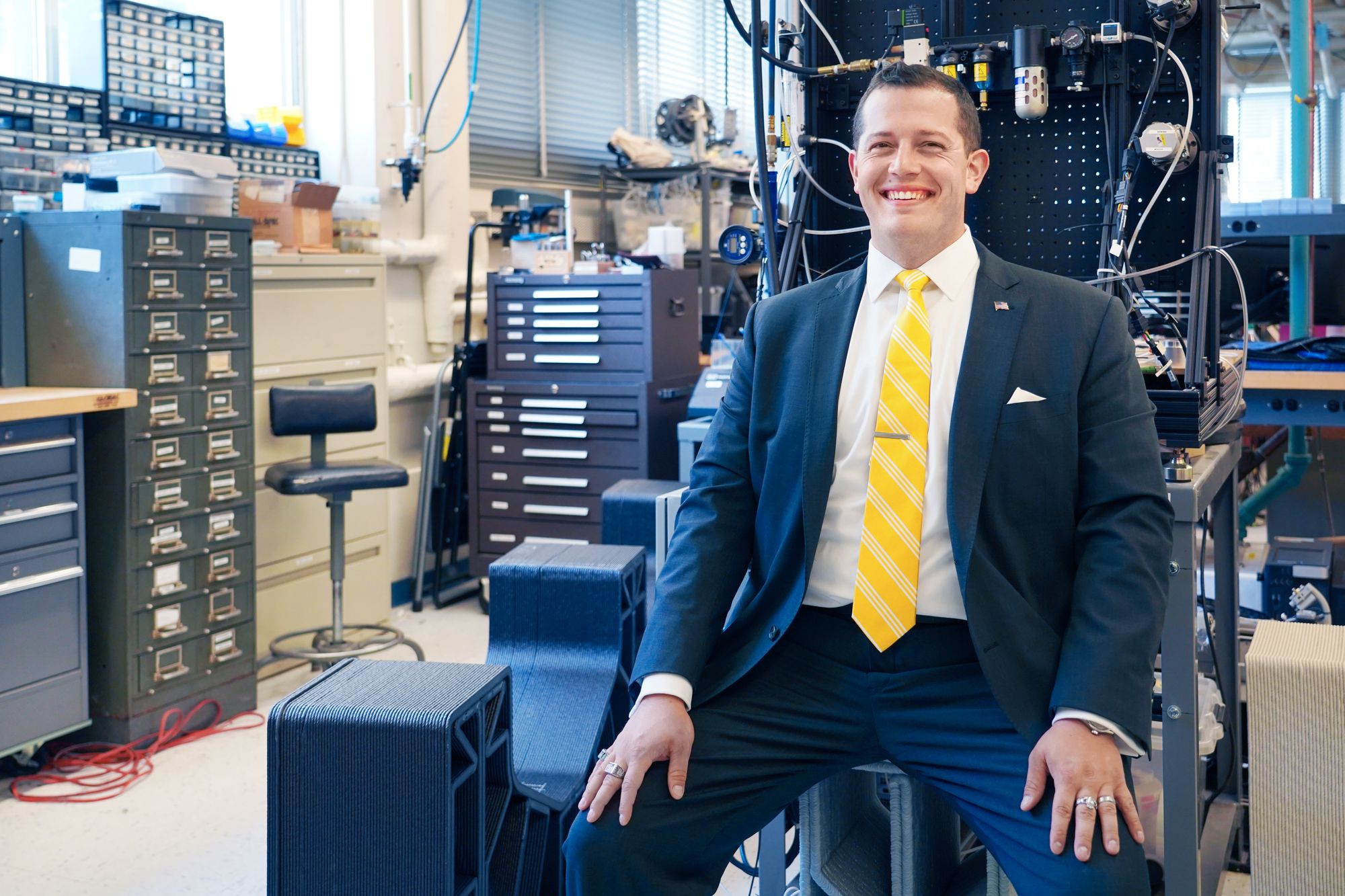
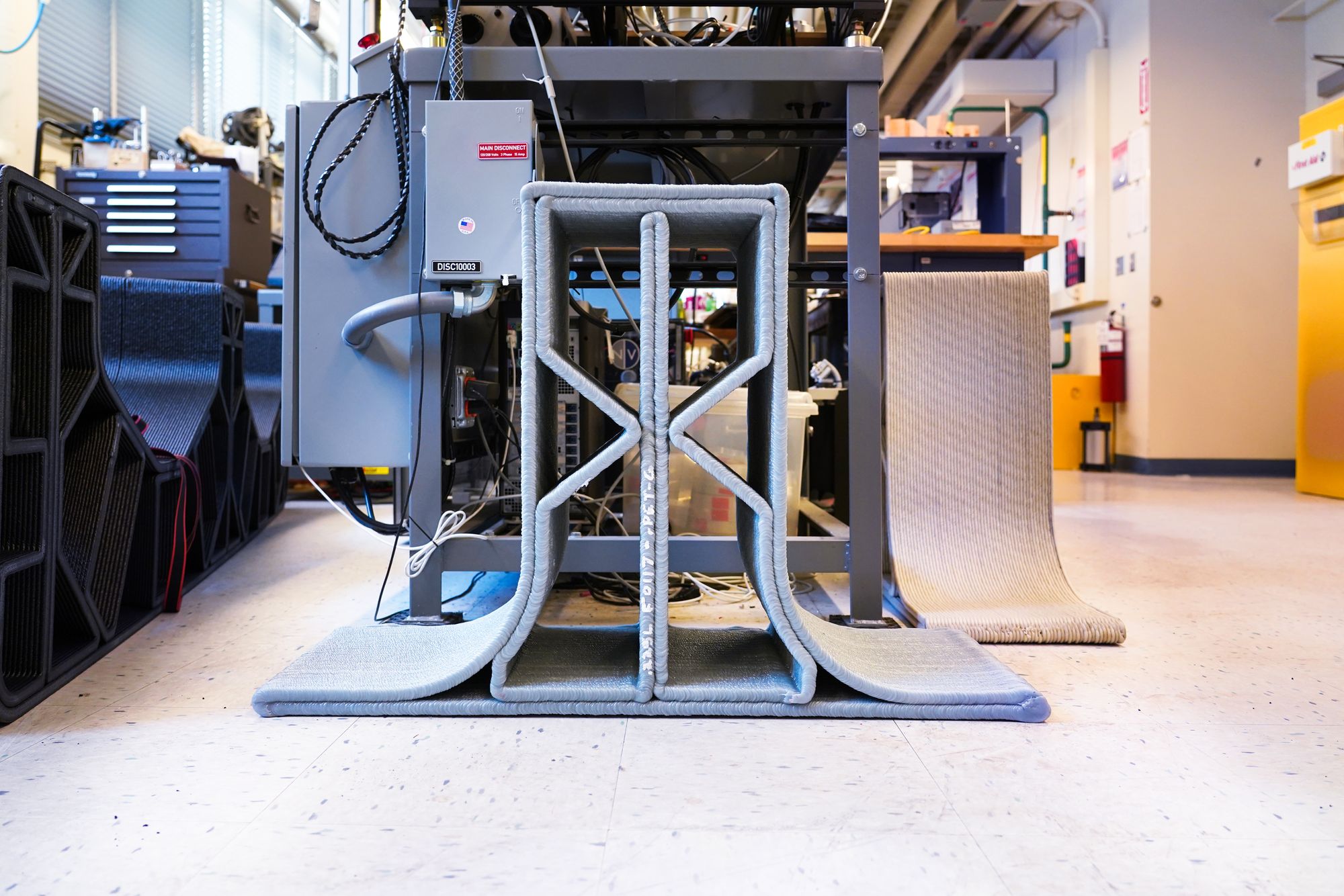
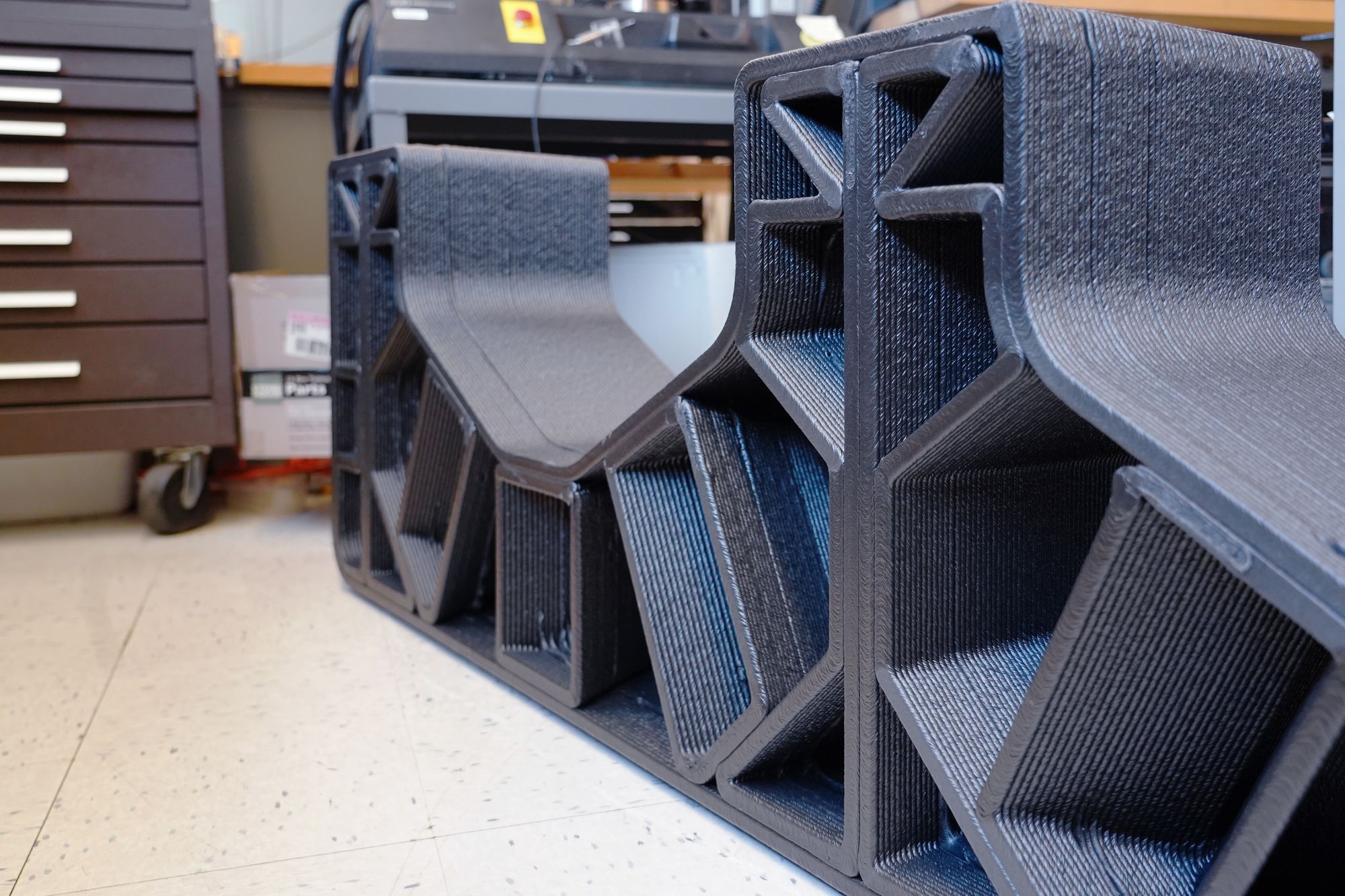
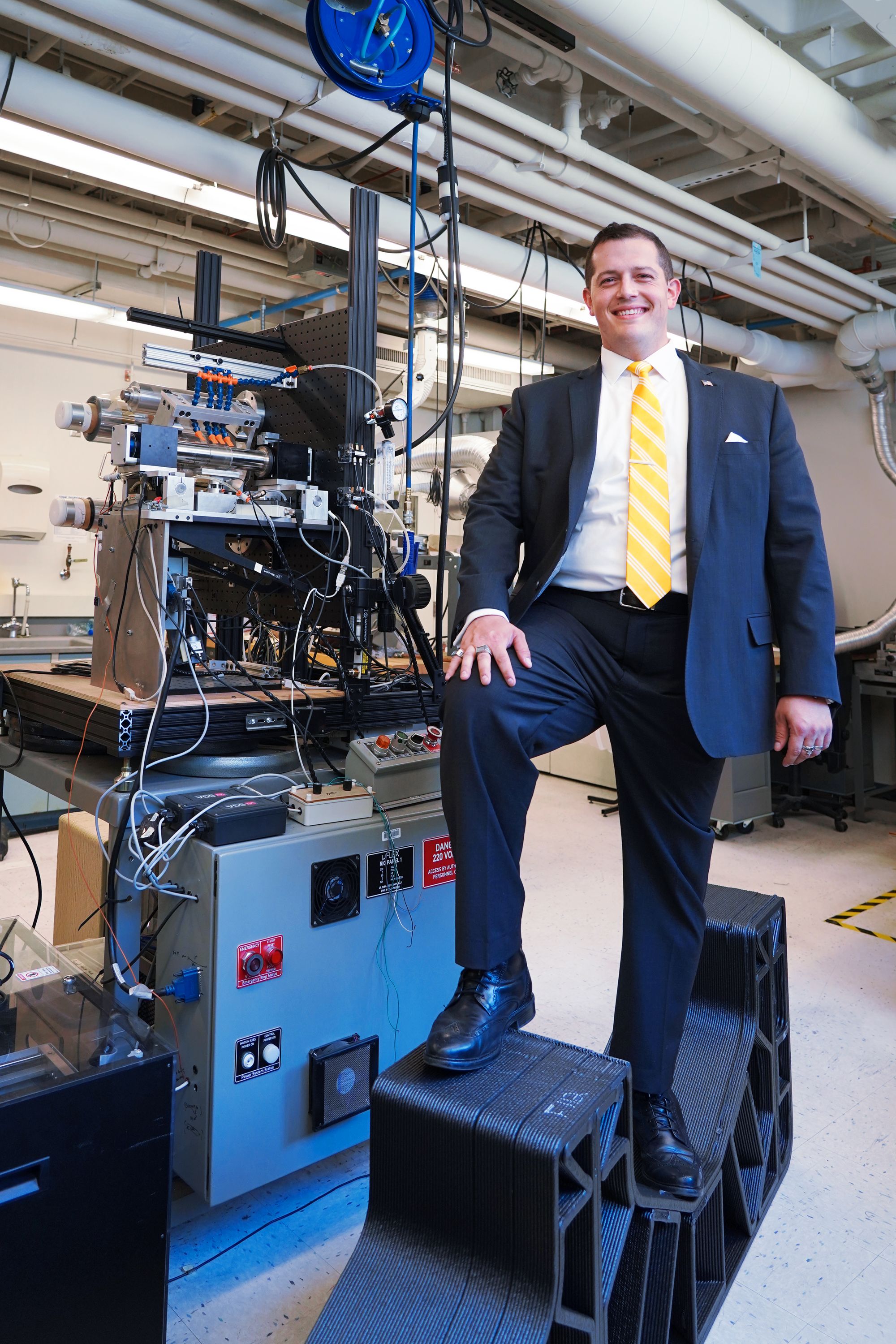
Could the world’s enormous mass of plastic waste become a building source for homes for people in need? AJ Perez, PhD, has developed a 3D-printed house foundation using recycled plastic bottles as part of a project exploring the viability of using the material to create affordable housing. Over the next year, the 2023 Chandler Fellowship will allow the work to continue with the establishment of a recycled-plastic microfactory research lab at MIT.
By Denise Brehm
May 5, 2023
The world’s population used 481.6 billion plastic bottles last year, creating mountains of waste on a massive scale. At the same time, more than a billion people worldwide have inadequate housing. These two troubling statistics may appear disparate, but for 2023 MechE PhD and MIT Morningside Academy for Design (MAD) 2022 Fellow AJ Perez, PhD, the former is a potential solution for the latter.
“Plastic doesn’t degrade, it’s hydrophobic, it’s self-extinguishing, and sadly, it’s everywhere,” says Perez, ticking off some of the desirable qualities of a good building material. As an expert in the area of 3D printing — his MIT spinoff, NVBOTS, developed 3D printers that could receive, store and print sequential jobs quickly and without the need of an onsite operator — Perez worried that the polymers used in many of these printers represent another unforeseen waste problem for future generations.
If you asked prominent inventors of now-commonly disposed objects, they might wish they had never invented these things, because of the waste and/or environmental damage they create.
What if, he wondered, we could substitute recycled plastic for virgin polymer? His thinking went further: Could recycled bottles become an inexpensive building material for houses that could be 3D printed across a distributed network of microfactories sited in the very areas where housing needs are the greatest?
As a doctoral student in mechanical engineering, Perez recently completed the first important step in proving the viability of this concept. For his PhD thesis project, Perez 3D printed, using the equivalent of about 15,000 plastic bottles, a prefabricated home foundation module weighing just under 300 pounds. The prototype withstood a load exceeding 60,000 pounds, more than 10 times the 6,000 pounds needed to support an 8-by-10 foot building.
Perez conducted this work as a member of the research group MIT HAUS, which was formed by Perez and his research advisor, Professor David Hardt of mechanical engineering, head of the department’s Master of Advanced Manufacturing and Design Program. Working with them on the 3D printed foundation — and on other parts of a planned 3D-printed home — was a cohort of eight undergraduates this spring, and many other undergraduates over the past few years. To 3D print the 8 feet long, 2 feet high, 1 foot wide foundation, Perez needed a 3D printer larger than any at MIT.
So he paid for time on an industrial 3D printer at a factory in another state for the five-hour print job. Back at MIT after his road trip pulling a U-Haul trailer, Perez used a lab in the Department of Civil and Environmental Engineering and, with the help of Stephen Rudolph, CEE lab manager and technical instructor, tested the strength of the foundation.
With the proof of concept now established, Perez said that much research remains to address long-term concerns of using recycled plastic as a building material, not just for foundations, but for entire homes. These include the effects of temperature extremes, direct sunshine, speed of printing, as well as making certain the material itself remains benign in real-world conditions.
“We’re not talking about simple shelters,” says Perez. “These could be permanent attractive homes for people who are either unhoused or underhoused.” He envisions mass manufacturing custom 8-by-10 tiny homes that are modular, expandable, connectable and even stackable. The sustainable homes would be printed locally, creating jobs in recycling, 3D-factory printing, and construction, in some of the world’s poorest communities.
With five companies already under his belt, Perez is not likely to stop with his feasibility assessment. In fact, the Department of Mechanical Engineering on April 19 awarded the MIT HAUS project the 2023 Chandler Fellowship (also known as the Health of the Planet Fellowship), money that will provide essential funding to build a recycled-plastic microfactory research lab. This builds upon the MIT Morningside Academy for Design Fellowship, which allowed Perez to forge ahead with his work over the past year.
“Without the MAD Fellowship, this research would not have been funded,” says Perez, who “learned from other MAD Fellows of very different disciplines. Not only technical information but also from hearing about their experiences as designers and the way they navigate different contexts in different countries.”
Being a Design Fellow is also about being an inspiration to future designers and encouraging people to pursue and build their dreams. Solutions exist that we just haven’t figured out. We need to get the right people in the right room to develop the ideas at the right time in the right place.
Perez, PhD, who holds a BS in mechanical engineering and MEng in advanced manufacturing and design from MIT, says he was “deeply inspired by a class taught by Maria Yang,” professor of mechanical engineering and associate director of MIT MAD. Yang’s class gave him a better understanding of global poverty, he says.
Over the next year, the Chandler Fellowship will allow MIT HAUS to revamp its lab to turn it into a campus plastic-bottle recycling plant in the basement of building 35. This will produce the feedstock for 3D printing the first sustainable tiny home made from recycled plastic bottles. MIT HAUS will build the prototype and continue experimentation to, for instance, add crushed glass bottles to the mixture, determine cleanliness standards for the recyclables, as well as study the mechanics of the materials. In other words, says Perez, figure out how to design a better, faster, cheaper process and use more recycled plastic.
Feb 22, 2023
Jul 18, 2023
Jun 23, 2023